Technical approach: Mechanical embelishment (part 1)
- Diogo Costa
- 16 de jan. de 2018
- 7 min de leitura
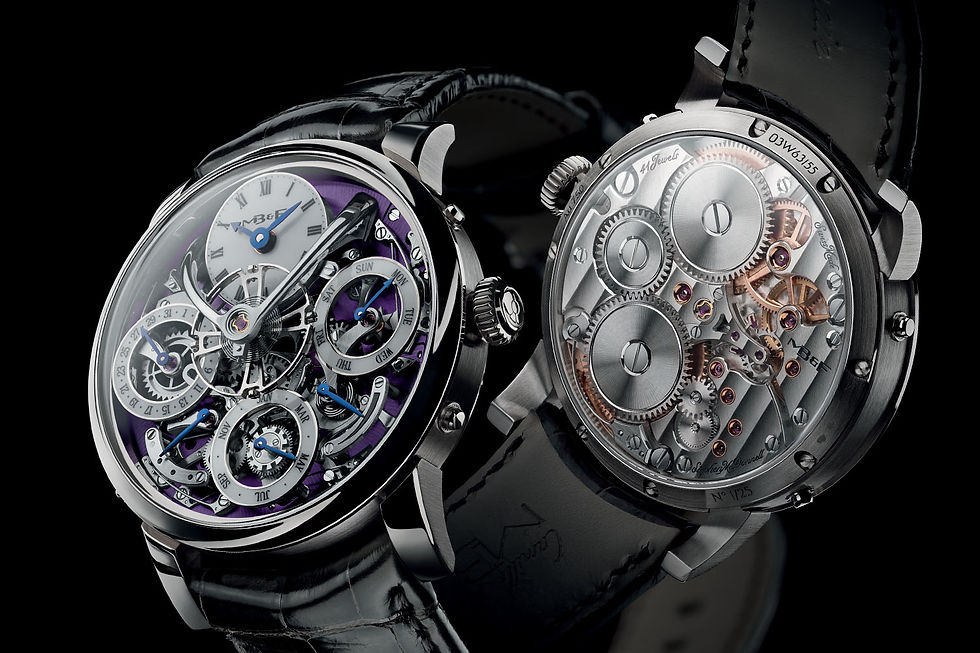
MB&F Legacy Machine Perpetual, limited to 25 pieces.
Last week I was scrolling my Facebook feed and suddenly I saw a post by a fellow watch enthusiast displaying different levels of mechanical finishing.
This led me to think about the obvious difficulty in understanding certain aspects of watchmaking, in this case, the decorative techniques.
To say it in a resumed way, if we don't know the correct name or meaning of something how can we perfectly understand it?
If there's a thing I've learned is that in horology specific terms are essential to correctly learn and understand about watches.
That's why it's so important to know such terms.
Introduction to the topic
Today I bring you one of the most curated lists of Haute Horlogerie I've made yet.
But to perfectly understand this topic I decided to split this article into two parts.
The first part is where we will learn how to identify certain aspects of high-end watchmaking or Haute Horlogerie.
Basically, in today's article, we will learn the theoretical info so on the second part of this article we can perfectly assimilate the information with the brands I've selected.
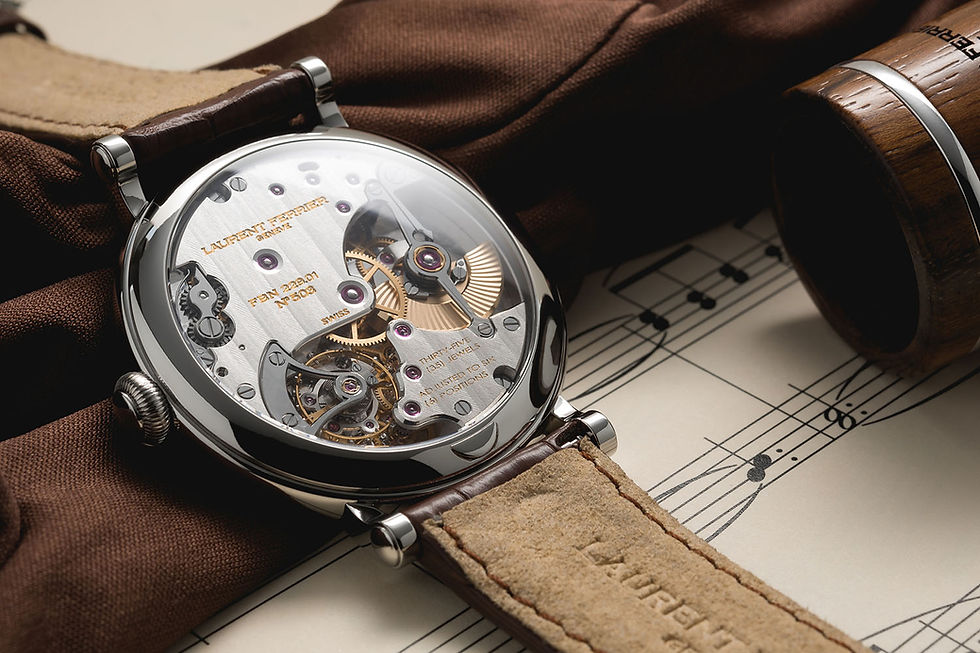
Laurent Ferrier Galet Micro Rotor
Decorating the mechanism and why it matters
In this list I will use a combination of two approaches, the first being an approach guided towards the visual and aesthetic part of the movement, and the second being the techincal and more specific approach.
Let's get started
The first aspects we need to cover, for a better understanding of this article, are the possible characteristics of mechanical embellishment.
Sinking
Cotes de Genève
Mirror polish
Engraving
Screw finishing
Perlage (circular graining)
Beveling or chamfering
Circular graining
Solarization
Straight graining
(Don't worry if you can't immediately relate the name to the aspect of the decoration, I will explain what are these techniques and how they're made throughout the article.)
Why decorating the movement matters?
In the end, the interest of a well-cared mechanism plays an essential role in modern days independent brands.
It doesn't only shows dedication in presenting clients with an exceptional quality but also shows how passionate is the person behind the brand.
And most importantly, how passionate is the watchmaker.
But let me warn you about something that can lead many people to error when trying to evaluate or analyse a certain timepiece.
When we have brands that produce watches in different price ranges it's normal to don't always have the same level of decoration, since the decorative techniques are expensive and take a quite large amount of time to apply.
So don't think that just because a certain brand produces a mechanism with sinking, engraving, Cotes de Genève and mirroring they do it in every single model.
Back to the explanation of the techniques.
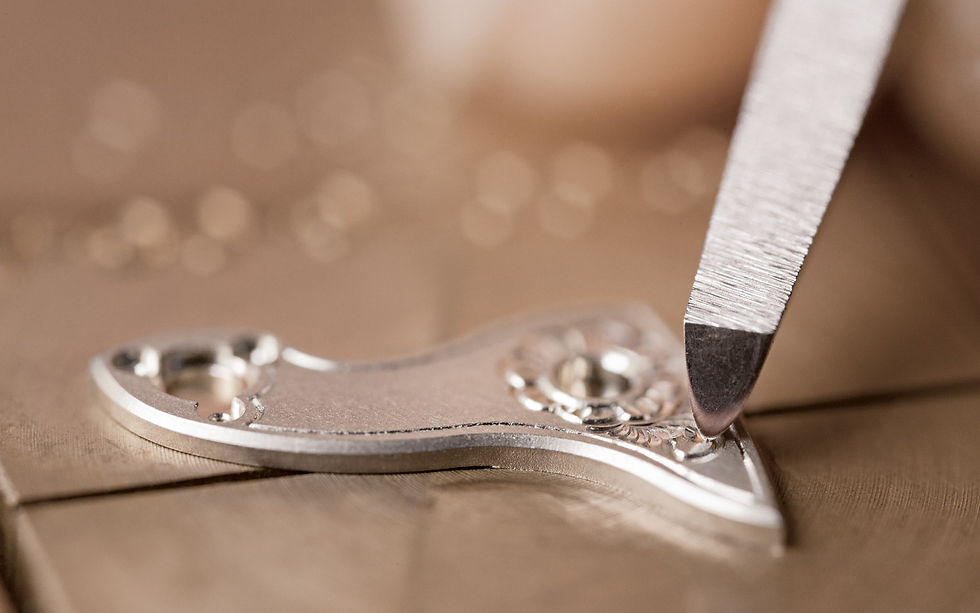
Engraving
Engraving is the hollowing or creating a relief in the material, by hand or machine.
Although it's a beautiful technic, its used mainly to show the hallmark, name of the watch or in some cases the name of the watchmaker itself (signature).
Believe it or not, there's a difference between hand engraving and machine-made engraving.
The major difference is the contrast between light and shadows that the hand engraving allows, while machine-made engraving is much more superficial.
If you ask me, the usage of the engraving technics must be well studied, so the mechanism continues to look simple for the eye to understand although its complexity, an excessive use of engraving might make the overall visual too tiring for the eye.
A nice example of the usage of the perfect amount of engraving is the MB&F Legacy Machine with the movement made by Kari Voutilainen.
This MB&F also makes use of another amazing technique, one that it's actually the most popular in the watch community nowadays which is the Cotes de Genève or Geneva stripes.
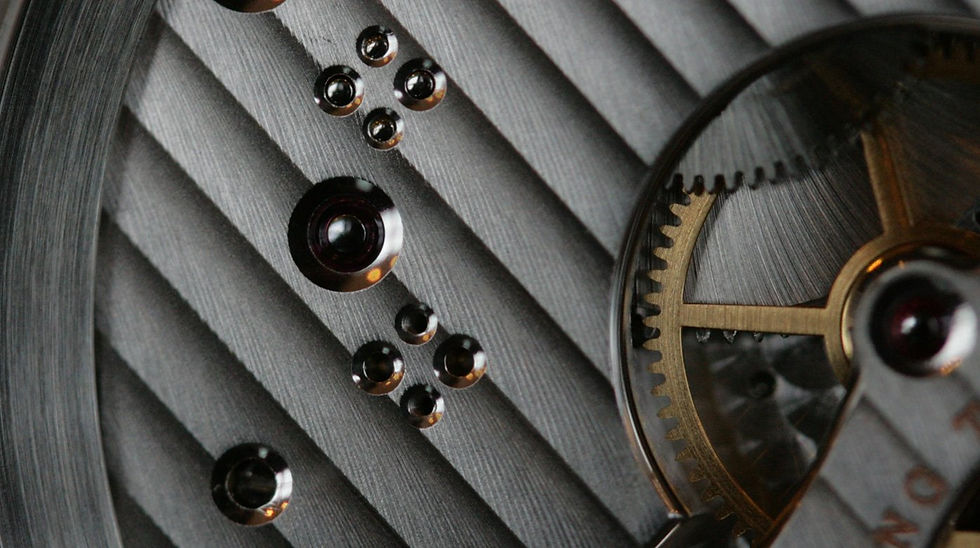
Cotes de Genève
The Cotes de Genève technique means that the watchmaker removes a certain amount of metal using a rotating abrasive tool at a inclined angle to create a parallel wave-like line pattern.
Using this technique makes the mechanism looks like a smooth continuous set of stripes that ultimately makes the totality of the movement stand out.
Although beautiful, this technique is only applied to non-moving parts due to the amount of material removed leading to non-regular surfaces that could influence the correct working and accuracy of the watch.
(It usually said that these stripes attract and retain the dust, protecting the working pieces from it.)
The final result of the Cotes de Genève technique is a genius game of lights and shadows due to the contrast of brushed stripes with a less brushed and almost polished outline.
But not every appliance of this technique looks perfectly the same, an example of this situation is the different visual aspects between the following two images.
While on the Laurent Ferrier we can see a matte looking finish on their Cotes de Genève and on an Audemars Piguet we have a more glossy looking usage of this pattern-like technique.
Apart from this visual differences, there's no wonder why this is one of the most popular techniques right!?

Mirror polish
Many people don't usually notice certain techniques due to its rather normal visual and this brings us to our next technique, the mirror polish.
In this case and from certain angles this type of polish might look like the part is made from a glossy black material, actually far from that.
The mirror polish is obtained due to time-consuming polishing where the watchmaker persues a perfectly smooth surface that has such a deep polish that reflects almost every light, making it look like a mirror.
Mirroring may go unnoticed, most times because people are used to observing a polished metal surface on almost every product made from this material leading to an association of normality and habituation.

Flat polishing
The technique of flat polishing is another extremely hard to use technique, the watchmakets needs to press the part in question against a coated with progressively finer diamond powder guiding the part in figures of eight.
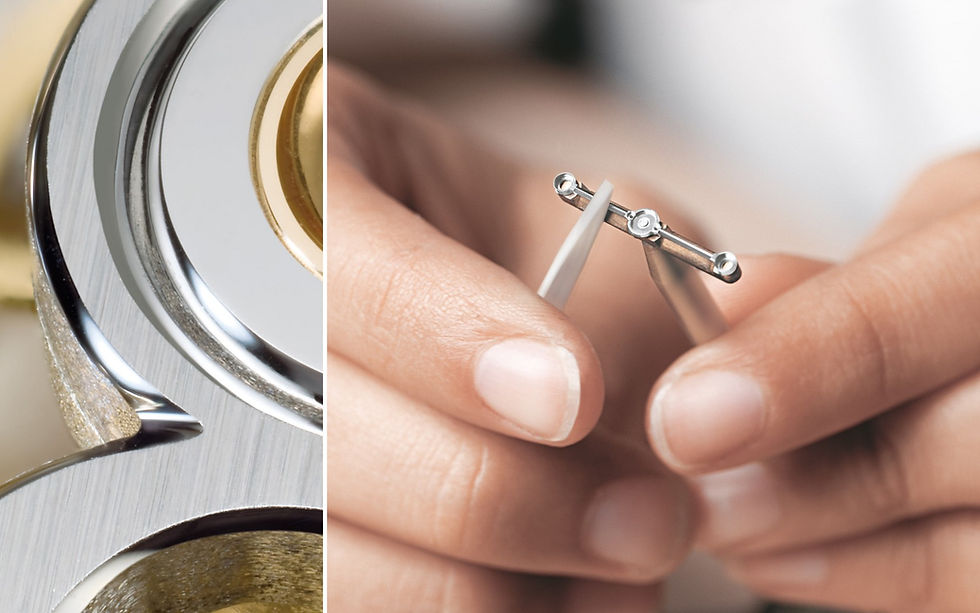
Beveling
I have to be honest, I reserved this article central space especially for my favorite technique, the beveling, also known as chamfering or anglage.
Beveling is the use of an abrasive tool to remove material from the edge of a certain part so it does an angle of 45 degrees (in general).
Apart from being one of the most complicated techniques, it has the objective of obtaining a regular polished beveled surface.
You might be asking yourself why this is my favorite technique.
It's simple, beveling is that one step that means hand-made, nothing can beat the beveling regarding on this aspect, the looking hand-made.
It also provides a tridimensional effect on the parts and a contrasting surface, as long as the regular surface of the part features a technique like Cotes de Genéve, this way creating contrast with the use of light reflection.

Perlage
Perlage is perhaps the hardest technique to apply and the most expensive too.
This technique is applied to both sides of the main plate and bridges. This amazing cloudy effect is obtained when using a rotative peg/tool.
Another interesting aspect of this technique is that each stipple overlaps the previous one, since the order of applying this technique is from the outside to the inside of the part, giviing it a similar hyptnotic look like the solarization (technique covered below).
In my opinion the Perlage almost makes the movement look tougher by looking more industrialized.
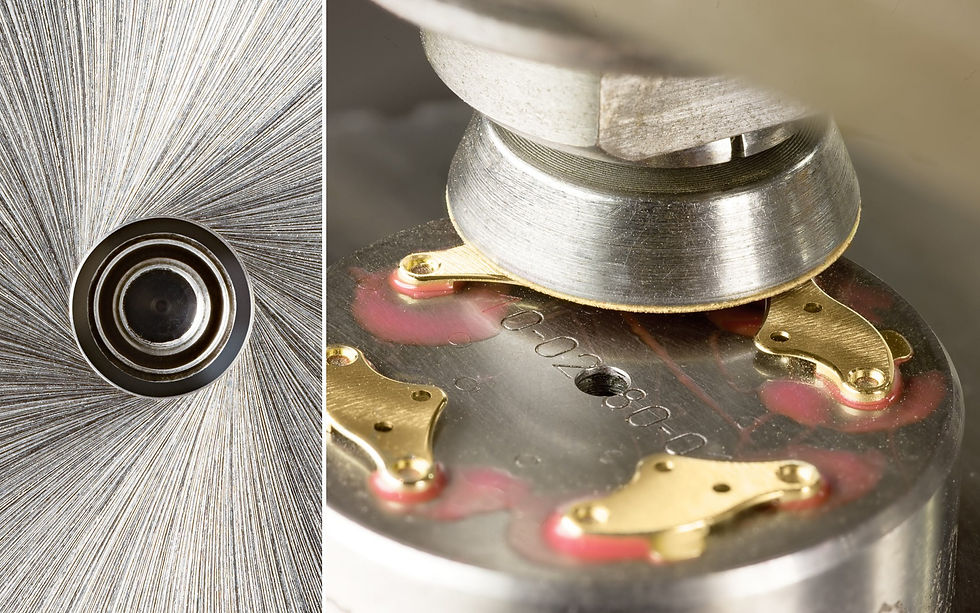
Solarization
When you notice a part feautring this technique I bet you have a vision of the pretty iconic Rolex dial, the sunburst dial.
This rotational effect is obtained when rotating the part and the grinding wheel in to opposite directions.
It's actually the most used technique in barrels and wheels.
Althought it's simplicty the rotational effect gives it detailed look that ends up being hypnotic.

Sinking
The next technique we're going to speak about is sinking.
Sinking is the creation of a concave chamfer where the screw takes a centralized position. Once again the beveling/chamfering makes it a detail that won't go unnoticed, and this concave chamfer can even be hand-polished!

Screws
As you might know, in watchmaking, that by itself its already an art with a very peculiar interest on detail, watchmakers think of everything, even the screws are taken seriously as an essential part of the movement, this said screws normally are hand-polished and to make them better and resilient they go through a treatment where a certain temperature is applied to obtain a perfect balance between resilience to time and hardness.
Although this choice is most times made with a visual aspect in mind and not with the objective of upgrading the composition of the screw itself.
Within this heat treatment, the screws can turn into several colors, each color meaning a different ratio of hardness and resilience.
The most common and balanced option is the blue colored screws that allow a perfect aging of the part and hardness.
One thing that most times we don't realize is that this technique can generate other colors if you choose to change the characteristics of the watch if you see fit. They can feature a yellowish color, a purple color, and even a green color, each color means a ratio/level of hardness.
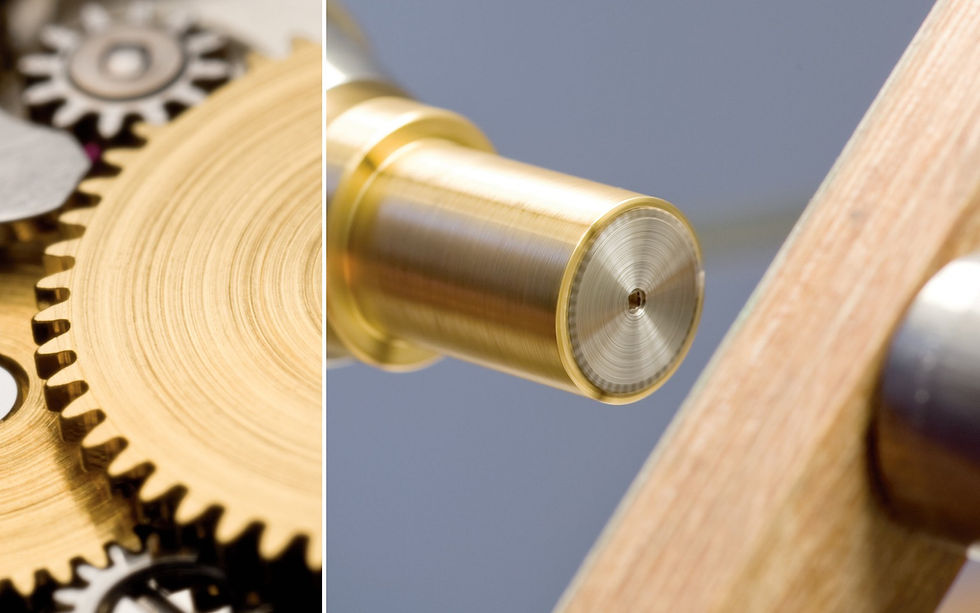
Circular graining
Another technique that nobody usually notices is the circular graining, which is used regularly on multiple gears.
Its made by rotating the part when pressing it against an abrasive film or paper.

Straight graining
This leads us into, once again, another variation of graining, the straight graining,
which is the result of a longitudunal movement when pressing the part into an abrasive paper to obtain straight lines.
This type of graining is mainly used in clicks and springs.
And that's it! It's fair to say that you can know better identify each of these techniques on your next journey to an AD or watch event!
But most importantly after reading this article, I hope we can better understand how watchmaking truly works by acknowledging the correct meaning of the terms related to it.
I hope you enjoyed reading this article.
In case you have doubts or question please feel free to comment or send me an email, I will happily reply!
Accurately yours,
Diogo
Hozzászólások